KBS maintenance is a critical process that ensures the smooth operation of equipment and systems, preventing unexpected breakdowns and costly repairs. In today's fast-paced industrial environment, businesses rely heavily on their machinery to meet production demands. However, without proper maintenance, even the most advanced systems can fail, leading to downtime and lost revenue. By implementing a structured KBS maintenance program, organizations can significantly reduce operational risks and enhance overall efficiency. This article delves into the nuances of KBS maintenance, providing actionable insights and strategies to help you optimize your maintenance processes.
Understanding the importance of KBS maintenance requires a closer look at its role in prolonging the lifespan of equipment and reducing operational costs. Regular maintenance not only keeps machinery running smoothly but also helps identify potential issues before they escalate into major problems. This proactive approach can save businesses thousands of dollars in repair costs and downtime. Furthermore, maintaining equipment according to manufacturer guidelines ensures compliance with safety regulations, protecting both employees and the environment.
As industries continue to evolve, so do the methods and technologies used for KBS maintenance. From predictive analytics to IoT-enabled sensors, modern tools offer unprecedented insights into equipment performance. However, implementing these advanced solutions requires a deep understanding of maintenance principles and a commitment to continuous improvement. In this article, we will explore the various aspects of KBS maintenance, including its benefits, challenges, and best practices. Whether you're a seasoned professional or just starting your journey in maintenance management, this guide will provide valuable insights to enhance your knowledge and skills.
Read also:Hozier
What Is KBS Maintenance?
KBS maintenance refers to the systematic process of maintaining and servicing equipment and systems to ensure their optimal performance and longevity. The term "KBS" stands for Knowledge-Based Systems, which are computerized systems that use artificial intelligence and expert systems to assist in decision-making processes. In the context of maintenance, KBS maintenance involves leveraging advanced technologies to predict, diagnose, and resolve issues before they impact operations. This approach differs from traditional maintenance methods, which often rely on scheduled inspections and reactive repairs.
The primary goal of KBS maintenance is to minimize downtime and improve operational efficiency by using data-driven insights. By integrating sensors, IoT devices, and machine learning algorithms, organizations can monitor equipment performance in real-time and receive alerts when anomalies are detected. This proactive approach allows maintenance teams to address issues promptly, reducing the likelihood of catastrophic failures. Additionally, KBS maintenance helps organizations optimize their maintenance schedules, ensuring that resources are allocated efficiently and effectively.
One of the key advantages of KBS maintenance is its ability to adapt to changing conditions. As equipment ages or operating conditions vary, the system can learn and adjust its maintenance recommendations accordingly. This flexibility ensures that maintenance activities remain relevant and effective over time. Furthermore, KBS maintenance promotes a culture of continuous improvement by encouraging organizations to analyze performance data and identify areas for enhancement. By embracing this innovative approach, businesses can achieve greater reliability and profitability in their operations.
Why Is KBS Maintenance Important?
The importance of KBS maintenance cannot be overstated, as it plays a crucial role in maintaining the health and performance of critical systems. Without proper maintenance, equipment can degrade rapidly, leading to unexpected failures and costly repairs. In some cases, these failures can result in significant safety hazards, putting employees and the surrounding environment at risk. By implementing KBS maintenance, organizations can mitigate these risks and ensure a safer, more reliable working environment.
Another critical aspect of KBS maintenance is its impact on operational costs. Regular maintenance helps extend the lifespan of equipment, reducing the need for frequent replacements. Additionally, by addressing issues before they escalate, organizations can avoid the high costs associated with emergency repairs and downtime. Over time, these savings can translate into substantial financial benefits, allowing businesses to allocate resources more effectively and improve their bottom line.
How Does KBS Maintenance Differ From Traditional Methods?
Traditional maintenance methods typically rely on scheduled inspections and reactive repairs, which can be inefficient and resource-intensive. In contrast, KBS maintenance leverages advanced technologies to provide a more proactive and data-driven approach. By continuously monitoring equipment performance and analyzing trends, KBS systems can predict potential issues before they occur, allowing maintenance teams to take preventive action. This predictive capability sets KBS maintenance apart from traditional methods and offers numerous advantages in terms of efficiency and reliability.
Read also:Beloit Scanner
Key Components of an Effective KBS Maintenance Program
An effective KBS maintenance program consists of several key components that work together to ensure the optimal performance of equipment and systems. These components include data collection, analysis, decision-making, and execution. By integrating these elements into a cohesive framework, organizations can create a maintenance program that addresses both current and future needs.
Data collection is the foundation of any KBS maintenance program, as it provides the raw material for analysis and decision-making. Modern systems use a variety of sensors and IoT devices to gather data on equipment performance, environmental conditions, and operational parameters. This data is then transmitted to a central database, where it can be analyzed using advanced algorithms and machine learning models. By identifying patterns and anomalies in the data, organizations can gain valuable insights into equipment behavior and potential issues.
Once data has been collected and analyzed, the next step is decision-making. KBS maintenance systems use expert systems and artificial intelligence to evaluate the data and recommend appropriate actions. These recommendations may include scheduling maintenance tasks, ordering replacement parts, or adjusting operational parameters. By automating this decision-making process, organizations can ensure that maintenance activities are timely and effective.
- Data collection using sensors and IoT devices
- Analysis of performance data using advanced algorithms
- Decision-making through expert systems and AI
- Execution of maintenance tasks based on recommendations
Challenges in Implementing KBS Maintenance
While KBS maintenance offers numerous benefits, implementing this approach can present several challenges. One of the primary obstacles is the initial investment required to install and configure the necessary hardware and software. Organizations must also invest in training their staff to use these advanced systems effectively. Additionally, integrating KBS maintenance into existing workflows can be complex, requiring careful planning and coordination.
Another challenge is the need for high-quality data to ensure accurate predictions and recommendations. Poor data quality can lead to incorrect conclusions and ineffective maintenance decisions. To address this issue, organizations must establish robust data governance practices and invest in data cleansing and validation tools. Furthermore, as KBS maintenance systems rely on machine learning algorithms, they require continuous updates and retraining to maintain their accuracy and relevance.
How Can Organizations Overcome These Challenges?
To overcome the challenges associated with KBS maintenance, organizations should adopt a phased implementation approach. This involves starting with a pilot program to test the system in a controlled environment and gradually expanding its scope as confidence and expertise grow. Additionally, organizations should prioritize data quality by implementing strict data governance policies and investing in data management tools. By addressing these challenges proactively, businesses can maximize the benefits of KBS maintenance while minimizing the risks.
What Are the Long-Term Benefits of KBS Maintenance?
In the long term, KBS maintenance can deliver significant benefits, including improved equipment reliability, reduced operational costs, and enhanced safety. By continuously monitoring and optimizing equipment performance, organizations can achieve greater efficiency and productivity. Furthermore, the data-driven insights provided by KBS maintenance systems enable businesses to make informed decisions about equipment upgrades and replacements, ensuring that their investments are aligned with strategic goals.
Best Practices for KBS Maintenance
Implementing best practices for KBS maintenance can help organizations maximize the effectiveness of their programs and achieve superior results. One of the most important best practices is to establish clear objectives and performance metrics. By defining what success looks like, organizations can measure the impact of their maintenance efforts and identify areas for improvement. Additionally, fostering a culture of continuous improvement encourages employees to embrace new technologies and processes, driving innovation and growth.
Another best practice is to leverage collaboration and communication across departments. By involving stakeholders from various functions, organizations can ensure that maintenance activities are aligned with broader business goals. Regular meetings and workshops provide opportunities for sharing knowledge and experiences, helping to build a collective understanding of KBS maintenance principles and practices. Finally, organizations should invest in ongoing training and development to ensure that their staff remains up-to-date with the latest technologies and techniques.
Tools and Technologies for KBS Maintenance
A wide range of tools and technologies are available to support KBS maintenance programs, from simple sensors to complex machine learning platforms. These tools enable organizations to collect, analyze, and act on data in real-time, ensuring that maintenance activities are timely and effective. Some of the most popular tools include:
- IoT-enabled sensors for monitoring equipment performance
- Data analytics platforms for processing and interpreting large datasets
- Machine learning algorithms for predicting equipment failures
- Mobile applications for accessing maintenance information on the go
When selecting tools and technologies for KBS maintenance, organizations should consider factors such as scalability, ease of use, and integration with existing systems. Additionally, they should prioritize solutions that offer strong security features to protect sensitive data and prevent unauthorized access.
Case Studies: Success Stories in KBS Maintenance
Several organizations have achieved remarkable success through the implementation of KBS maintenance programs. For example, a leading manufacturing company reduced its downtime by 40% after adopting a predictive maintenance approach powered by KBS technologies. Similarly, a utility provider improved its asset reliability by 30% by using IoT sensors and machine learning algorithms to monitor equipment performance. These success stories demonstrate the potential of KBS maintenance to transform operations and deliver tangible business value.
How Can These Success Stories Inspire Your Organization?
By studying the success stories of other organizations, businesses can gain valuable insights into the potential benefits of KBS maintenance and the strategies required to achieve them. These case studies provide real-world examples of how KBS maintenance can be applied in various industries and contexts, helping organizations to tailor their programs to their specific needs and challenges. Additionally, they highlight the importance of collaboration, innovation, and continuous improvement in driving success.
Frequently Asked Questions
What Are the Common Misconceptions About KBS Maintenance?
One common misconception about KBS maintenance is that it requires a complete overhaul of existing systems and processes. In reality, KBS maintenance can be implemented incrementally, allowing organizations to integrate new technologies and techniques without disrupting their operations. Another misconception is that KBS maintenance is only suitable for large enterprises with extensive resources. However, with the growing availability of affordable tools and platforms, even small and medium-sized businesses can benefit from this approach.
How Often Should KBS Maintenance Be Performed?
The frequency of KBS maintenance depends on several factors, including the type of equipment, operating conditions, and organizational goals. In general, KBS maintenance should be performed regularly to ensure that equipment remains in optimal condition. However, the specific schedule will vary based on the recommendations of the manufacturer and the insights provided by the KBS system. By continuously monitoring equipment performance, organizations can adjust their maintenance schedules as needed to achieve the best results.
Conclusion
KBS maintenance represents a revolutionary approach to equipment management, offering numerous benefits for organizations across industries. By leveraging advanced technologies and data-driven insights, businesses can achieve greater reliability, efficiency, and safety in their operations. While implementing KBS maintenance may present some challenges, the long-term benefits far outweigh the initial investment. By adopting best practices, selecting the right tools and technologies, and learning from success stories, organizations can unlock the full potential of KBS maintenance and drive sustainable growth.
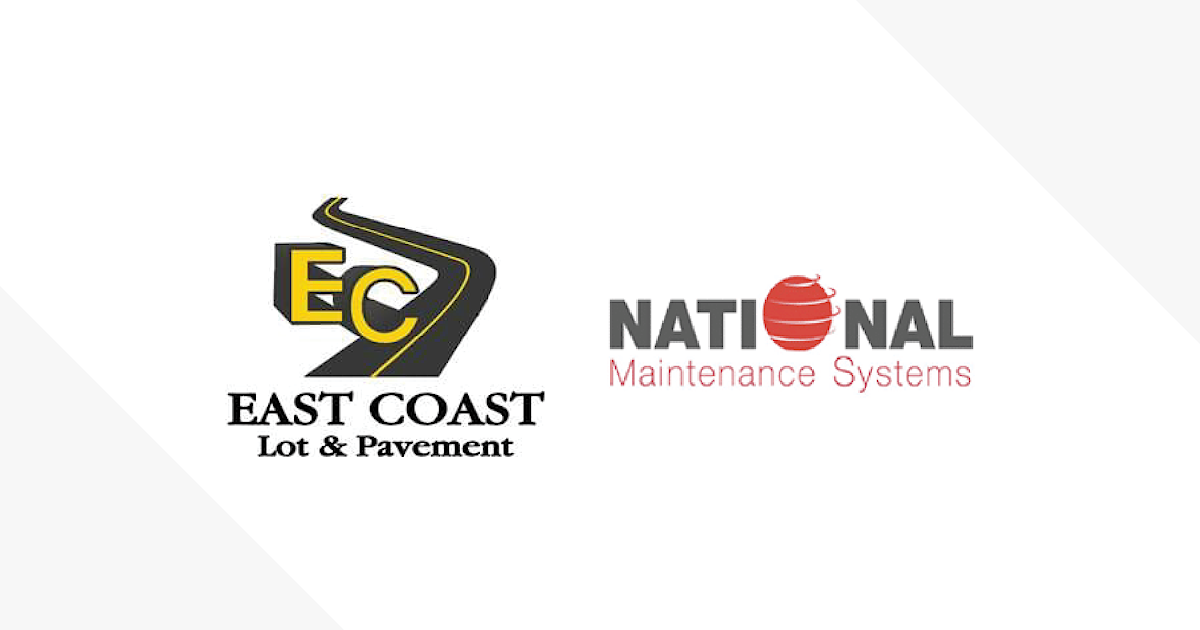
